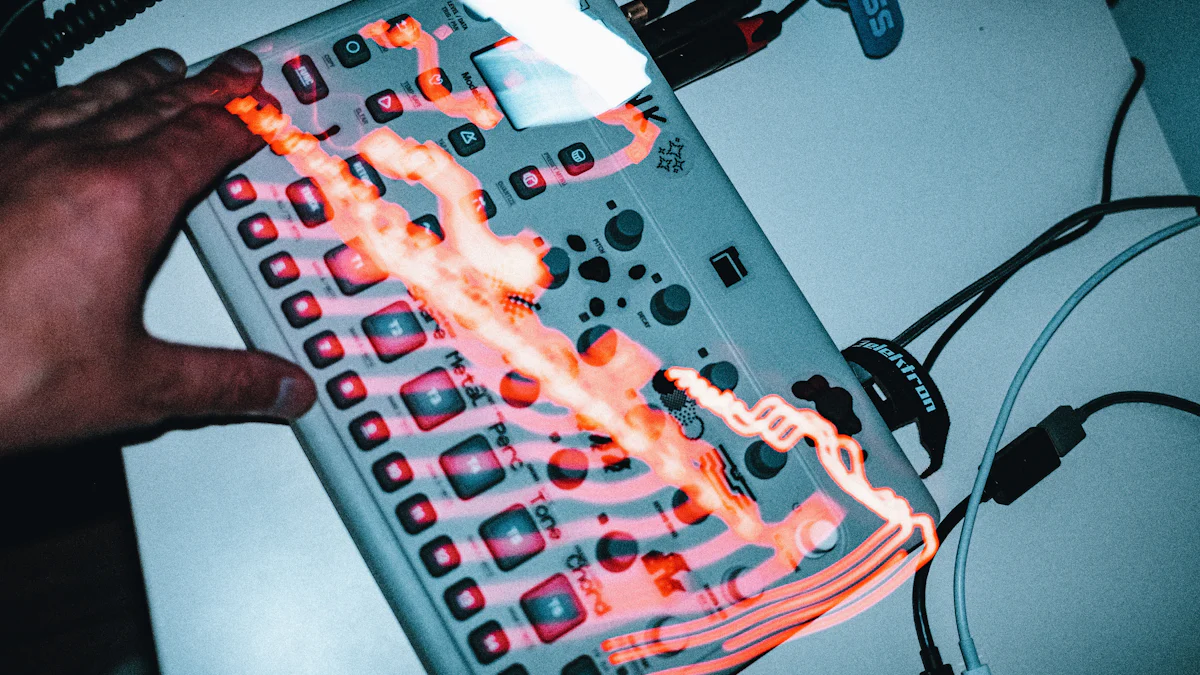
I have observed that rechargeable batteries made are primarily manufactured in countries like China, South Korea, and Japan. These nations excel due to several factors that set them apart.
- Technological advancements, such as the development of lithium-ion and solid-state batteries, have revolutionized battery performance.
- Government support for renewable energy projects has created a favorable environment for production.
- The increasing adoption of electric vehicles has further fueled demand, with governments offering incentives to promote this shift.
These elements, combined with robust supply chains and access to raw materials, explain why these countries lead the industry.
Key Takeaways
- China, South Korea, and Japan make most rechargeable batteries. They have advanced tools and strong supply systems.
- The U.S. and Canada are making more batteries now. They focus on using local materials and factories.
- Being eco-friendly is very important for battery makers. They use green energy and safe methods to help the planet.
- Recycling helps cut waste and use fewer new materials. This supports reusing resources in a smart way.
- New technology, like solid-state batteries, will make batteries safer and better in the future.
Global Manufacturing Hubs for Rechargeable Batteries
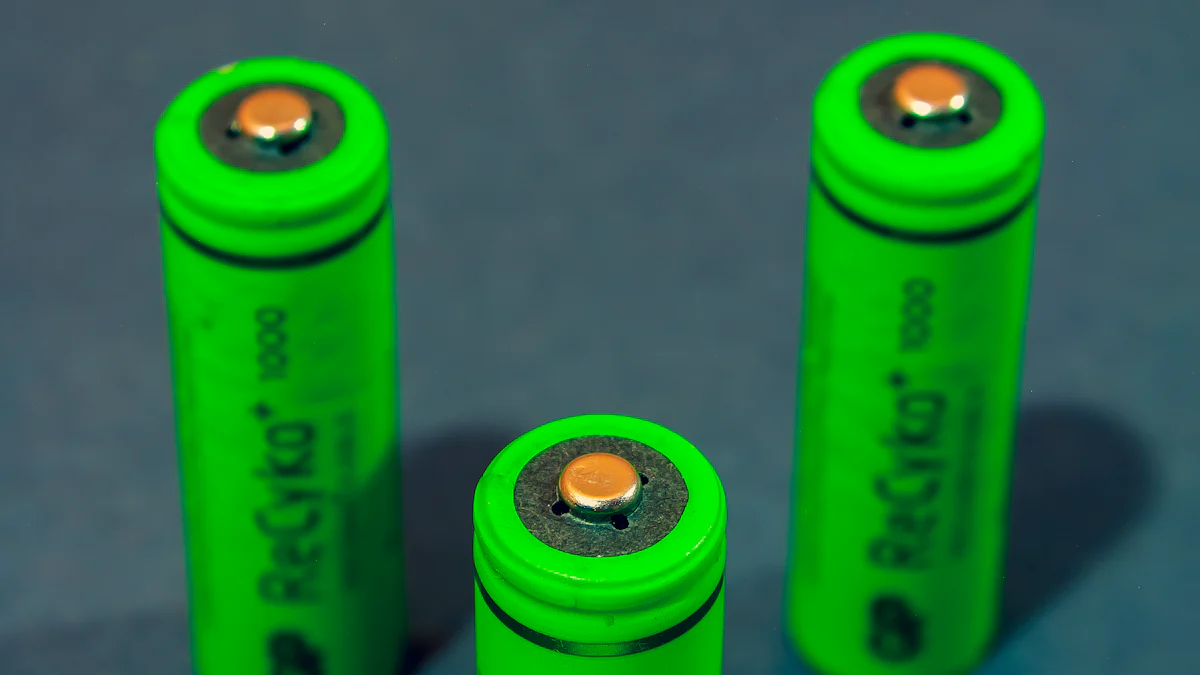
Asia’s Leadership in Battery Production
China’s dominance in lithium-ion battery manufacturing
I have observed that China leads the global market for lithium-ion batteries. In 2022, the country supplied 77% of the world’s rechargeable batteries. This dominance stems from its extensive access to raw materials like lithium and cobalt, coupled with advanced manufacturing capabilities. China’s government has also heavily invested in renewable energy and electric vehicle industries, creating a robust ecosystem for battery production. The scale of production in China ensures that rechargeable batteries made here remain cost-effective and widely available.
South Korea’s advancements in high-performance battery technology
South Korea has carved a niche in producing high-performance batteries. Companies like LG Energy Solution and Samsung SDI focus on developing batteries with superior energy density and faster charging capabilities. I find their emphasis on research and development impressive, as it drives innovation in the industry. South Korea’s expertise in consumer electronics further strengthens its position as a leader in battery technology.
Japan’s reputation for quality and innovation
Japan has built a reputation for producing high-quality rechargeable batteries. Manufacturers like Panasonic prioritize precision and reliability, which makes their products highly sought after. I admire Japan’s commitment to innovation, particularly in solid-state battery research. This focus on cutting-edge technology ensures that Japan remains a key player in the global battery market.
North America’s Expanding Role
The United States’ focus on domestic battery production
The United States has significantly increased its role in battery production over the past decade. Rising demand for electric vehicles and renewable energy storage has driven this growth. The U.S. government has supported the industry through initiatives and investments, leading to a doubling of renewable energy capacity from 2014 to 2023. California and Texas now lead in battery storage capacity, with plans to expand further. I believe this focus on domestic production will reduce reliance on imports and strengthen the U.S. position in the global market.
Canada’s role in raw material supply and manufacturing
Canada plays a crucial role in supplying raw materials like nickel and cobalt, essential for rechargeable batteries made worldwide. The country has also begun investing in battery manufacturing facilities to capitalize on its resource wealth. I see Canada’s efforts as a strategic move to integrate itself further into the global battery supply chain.
Europe’s Growing Battery Industry
The rise of gigafactories in Germany and Sweden
Europe has emerged as a growing hub for battery production, with Germany and Sweden leading the charge. Gigafactories in these countries focus on meeting the region’s increasing demand for electric vehicles. I find the scale of these facilities impressive, as they aim to reduce Europe’s dependence on Asian imports. These factories also emphasize sustainability, aligning with Europe’s environmental goals.
EU policies encouraging local production
The European Union has implemented policies to boost local battery production. Initiatives like the European Battery Alliance aim to secure raw material supplies and promote circular economy practices. I believe these efforts will not only enhance Europe’s production capacity but also ensure long-term sustainability in the industry.
Materials and Processes in Rechargeable Battery Production
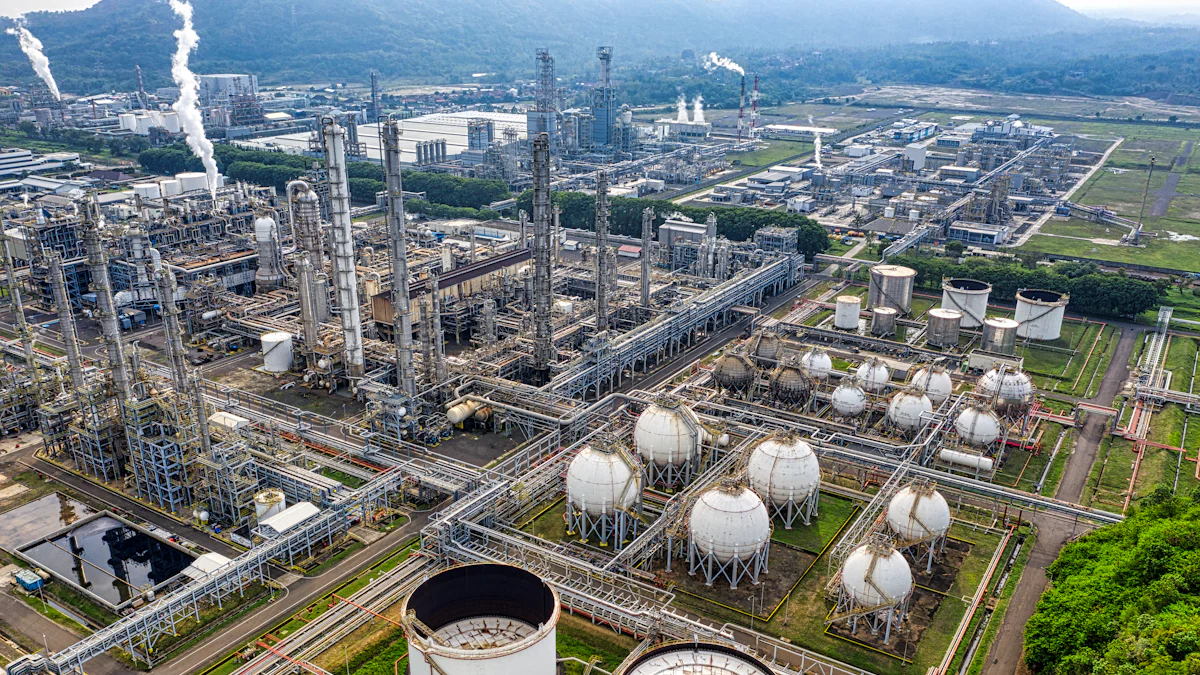
Essential Raw Materials
Lithium: A critical component of rechargeable batteries
Lithium plays a pivotal role in the production of rechargeable batteries. I have observed that its lightweight and high energy density make it indispensable for lithium-ion batteries. However, mining lithium comes with environmental challenges. Extraction processes often lead to air and water pollution, land degradation, and groundwater contamination. In regions like the Democratic Republic of the Congo, cobalt mining has caused severe ecological damage, while satellite analysis in Cuba has revealed over 570 hectares of land rendered barren due to nickel and cobalt mining activities. Despite these challenges, lithium remains a cornerstone of battery technology.
Cobalt and nickel: Key to battery performance
Cobalt and nickel are essential for enhancing battery performance. These metals improve energy density and longevity, making them critical for applications like electric vehicles. I find it fascinating how these materials contribute to the efficiency of rechargeable batteries made globally. Yet, their extraction is energy-intensive and poses risks to local ecosystems and communities. Toxic metal leaks from mining operations can harm both human health and the environment.
Graphite and other supporting materials
Graphite serves as the primary material for battery anodes. Its ability to store lithium ions efficiently makes it a vital component. Other materials, such as manganese and aluminum, also play supporting roles in improving battery stability and conductivity. I believe these materials collectively ensure the reliability and performance of modern batteries.
Key Manufacturing Processes
Mining and refining of raw materials
The production of rechargeable batteries begins with mining and refining raw materials. This step involves extracting lithium, cobalt, nickel, and graphite from the earth. Refining these materials ensures they meet the purity standards required for battery manufacturing. Although this process is energy-intensive, it lays the foundation for high-quality batteries.
Cell assembly and battery pack production
Cell assembly involves several intricate steps. First, active materials are mixed to achieve the right consistency. Then, slurries are coated onto metal foils and dried to form protective layers. The coated electrodes are compressed through calendaring to enhance energy density. Finally, the electrodes are cut, assembled with separators, and filled with electrolytes. I find this process fascinating due to its precision and complexity.
Quality control and testing procedures
Quality control is a critical aspect of battery manufacturing. Effective inspection methods are essential to detect defects and ensure reliability. I have noticed that balancing quality with production efficiency is a significant challenge. Defective cells escaping the factory can damage a company’s reputation. Therefore, manufacturers invest heavily in testing procedures to maintain high standards.
Environmental and Economic Implications of Rechargeable Battery Production
Environmental Challenges
Mining impacts and resource depletion
Mining for materials like lithium and cobalt creates significant environmental challenges. I have observed that lithium extraction, for instance, requires vast amounts of water—up to 2 million tonnes for just one tonne of lithium. This has led to severe water depletion in regions like the South American Lithium Triangle. Mining activities also destroy habitats and pollute ecosystems. Harmful chemicals used during extraction contaminate water sources, endangering aquatic life and human health. Satellite imagery reveals barren landscapes caused by nickel and cobalt mining, highlighting the long-term damage to local ecosystems. These practices not only degrade the environment but also accelerate resource depletion, raising concerns about sustainability.
Recycling and waste management concerns
Recycling rechargeable batteries remains a complex process. I find it fascinating how used batteries undergo multiple steps, including collection, sorting, shredding, and separation, to recover valuable metals like lithium, nickel, and cobalt. Despite these efforts, recycling rates remain low, leading to increased electronic waste. Inefficient recycling methods contribute to resource wastage and environmental pollution. Establishing efficient recycling programs could minimize waste and reduce the need for new mining operations. This would help address the growing environmental concerns associated with rechargeable battery production.
Economic Factors
Costs of raw materials and labor
The production of rechargeable batteries involves high costs due to the reliance on rare materials like lithium, cobalt, and nickel. These materials are not only expensive but also energy-intensive to extract and process. Labor costs further add to the overall expenses, especially in regions with stringent safety and environmental regulations. I believe these factors significantly influence the pricing of rechargeable batteries made globally. Safety concerns, such as the risks of explosion and fire, also increase production costs, as manufacturers must invest in advanced safety measures.
Global competition and trade dynamics
Global competition drives innovation in the rechargeable battery industry. Companies constantly develop new technologies to stay ahead. Pricing strategies must adapt to remain competitive in a market influenced by strategic partnerships and geographic expansions. I have noticed that emerging markets play a crucial role in shaping trade dynamics. Expanding production capacity in regions like North America and Europe not only reduces reliance on imports but also aligns with governmental policies promoting green technologies. This creates opportunities for job creation and economic growth.
Sustainability Efforts
Innovations in eco-friendly production methods
Sustainability has become a priority in battery manufacturing. I admire how companies are adopting eco-friendly production methods to reduce their environmental impact. For example, some manufacturers now use renewable energy sources to power their facilities. Innovations in battery design also focus on reducing the need for rare materials, making production more sustainable. These efforts not only lower carbon emissions but also contribute to a circular economy by promoting material reuse.
Policies promoting circular economy practices
Governments worldwide are implementing policies to encourage sustainable practices in battery production. Extended producer responsibility (EPR) mandates hold manufacturers accountable for managing batteries at the end of their lifecycle. Recycling targets and funding for research and development further support these initiatives. I believe these policies will accelerate the adoption of circular economy practices, ensuring that rechargeable batteries made today have a reduced environmental footprint. By prioritizing sustainability, the industry can achieve long-term growth while addressing environmental concerns.
Future Trends in Rechargeable Battery Manufacturing
Technological Advancements
Solid-state batteries and their potential
I see solid-state batteries as a game-changer in the industry. These batteries replace liquid electrolytes with solid ones, offering significant advantages. The table below highlights the key differences between solid-state and traditional lithium-ion batteries:
Feature | Solid-State Batteries | Traditional Lithium-Ion Batteries |
---|---|---|
Electrolyte Type | Solid electrolytes (ceramic or polymer-based) | Liquid or gel electrolytes |
Energy Density | ~400 Wh/kg | ~250 Wh/kg |
Charging Speed | Faster due to high ionic conductivity | Slower compared to solid-state |
Thermal Stability | Higher melting point, safer | Prone to thermal runaway and fire hazards |
Cycle Life | Improving, but generally lower than lithium | Generally higher cycle life |
Cost | Higher manufacturing costs | Lower manufacturing costs |
These batteries promise faster charging and improved safety. However, their high production costs remain a challenge. I believe advancements in manufacturing techniques will make them more accessible in the future.
Improvements in energy density and charging speed
The industry is making strides in enhancing battery performance. I find the following advancements particularly noteworthy:
- Lithium-sulfur batteries use lightweight sulfur cathodes, boosting energy density.
- Silicon anodes and solid-state designs are transforming energy storage for electric vehicles (EVs).
- High-power charging stations and silicon carbide chargers reduce charging times significantly.
- Bidirectional charging allows EVs to stabilize power grids and serve as backup energy sources.
These innovations ensure that rechargeable batteries made today are more efficient and versatile than ever before.
Expansion of Production Capacity
New gigafactories and facilities worldwide
The demand for batteries has led to a surge in gigafactory construction. Companies like Tesla and Samsung SDI are investing heavily in new facilities. For example:
- Tesla allocated $1.8 billion to R&D in 2015 to develop advanced lithium-ion cells.
- Samsung SDI expanded its operations in Hungary, China, and the U.S.
These investments aim to meet the growing need for EVs, portable electronics, and renewable energy storage.
Regional diversification to mitigate supply chain risks
I have noticed a shift toward regional diversification in battery production. This strategy reduces reliance on specific regions and strengthens supply chains. Governments worldwide are encouraging local manufacturing to enhance energy security and create jobs. This trend ensures a more resilient and balanced global battery market.
Sustainability as a Priority
Increased use of recycled materials
Recycling plays a crucial role in sustainable battery production. While many believe only 5% of lithium-ion batteries are recycled, economic incentives are driving change. Recycling valuable metals like lithium and cobalt reduces the need for new mining operations. I see this as a vital step toward minimizing environmental impact.
Development of green energy-powered factories
Manufacturers are adopting renewable energy to power their facilities. This shift lowers carbon emissions and aligns with global sustainability goals. I admire how these efforts contribute to a circular economy, ensuring that rechargeable batteries made today support a greener future.
Rechargeable batteries are primarily manufactured in Asia, with North America and Europe playing increasingly significant roles. I have observed that the production process depends on critical raw materials like lithium and cobalt, alongside advanced manufacturing techniques. However, challenges such as high fixed costs, reliance on rare materials, and supply security risks persist. Government policies, including safety standards and recycling guidelines, shape the industry’s direction. Sustainability efforts, such as adopting renewable energy and eco-friendly mining practices, are transforming the future of rechargeable batteries made today. These trends highlight a promising shift toward innovation and environmental responsibility.
FAQ
What are the main countries producing rechargeable batteries?
China, South Korea, and Japan dominate global battery production. The United States and Europe are expanding their roles with new facilities and policies. These regions excel due to advanced technology, access to raw materials, and strong supply chains.
Why is lithium important in rechargeable batteries?
Lithium offers high energy density and lightweight properties, making it essential for lithium-ion batteries. Its unique characteristics enable efficient energy storage, which is crucial for applications like electric vehicles and portable electronics.
How do manufacturers ensure battery quality?
Manufacturers use rigorous quality control processes, including defect detection and performance testing. Advanced inspection methods ensure reliability and safety, which are critical for maintaining customer trust and meeting industry standards.
What challenges does the battery industry face?
The industry faces challenges like high raw material costs, environmental concerns from mining, and supply chain risks. Manufacturers address these issues through innovations, recycling initiatives, and regional diversification.
How is sustainability shaping battery production?
Sustainability drives the adoption of eco-friendly methods, such as using renewable energy in factories and recycling materials. These efforts reduce environmental impact and align with global goals for a greener future.
Post time: Jan-13-2025